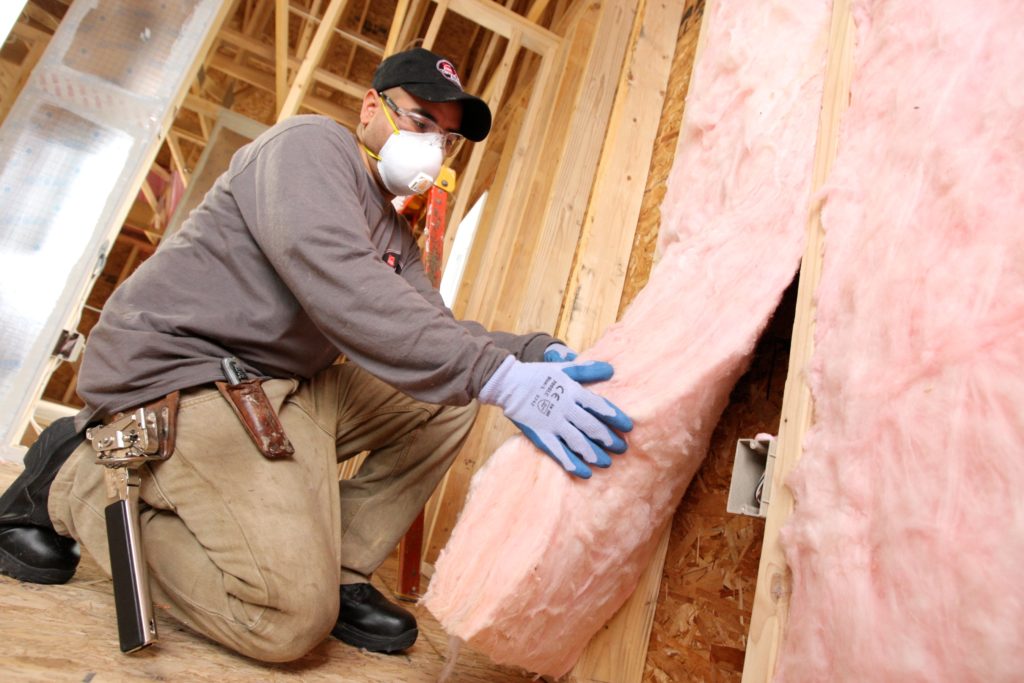
Fibreglass is a fibre-reinforced plastic material that can be moulded into different shapes and used in construction projects. Best fibreglass insulation is lightweight, insulates well, and has the ability to resist both fire and moisture.
Fibreglass insulation is most commonly made from glass granulate, short fibres of glass (known as fluff), or a combination of the two. The process starts by blending the raw materials together in a dusting machine that then sprays them through a range of small holes heated to over 400 degrees Fahrenheit (200 degrees Celsius).
The hot mixture is lowered into a mould and allowed to cool slowly. As it cools, the hot fibres bond with the cool fibres in a process called covalent bonding. The mixture then goes through several more steps to strengthen the material and make it waterproof.
Fibreglass insulation is most commonly used in industrial applications where its lightweight, high R-value, and fire resistance are valued by many users. A common application of fibreglass insulation is as a house wrap for walls and ceilings in European construction.
Materials needed
The most common materials used to make fibreglass insulation by glass fibre manufacturers are as follows ;
- short glass fibres are made by drawing molten glass through a hole and stretching it into a fine thread. The fibres are then baked to harden them, giving them their strength and rigidity.
- glass granules are small pieces of recycled glass that have been ground up into a fine powder. They add bulk to the material, increasing the insulation value of the finished product.
3 . Individual glass fibres and granules are mixed together in different ratios depending on the purpose of the insulation being produced.
- In a typical manufacturing process, the material is fed from a bin into a hopper where it is mixed with other agents and additives that may include binders and plasticizers.
- The material then passes through an airlock before being sprayed into an oven by a fiber duster, which can be varied in duration and pressure to control the density of the finished material.
- Once the insulation has been sprayed into the mold, it is removed once cool and ready to use.
- The insulation can then be recycled and reused for multiple applications.
- Glass fibre insulation is manufactured by a variety of equipment and techniques depending on the type.
- The finished material is then put into bagged or spray-in-place forms that are either pressure-sealed or vacuum-sealed.
Conclusion
Fibre Glass Insulation installation process through a shower wall, this is how insulation is installed prior to the drywall being attached to the studs.Glass fibers are mixed with short glass fibers to make the “glass matrix” of the insulation. Glass fibers themselves and granules are mixed with a binder such as polyvinyl acetate or polyvinyl alcohol, then mixed with other additives such as ultraviolet resistance and flame retardants. The resulting plastic compound is then laid out flat on a form or into moulds and allowed to dry. The mixture in the moulds is reduced to granules, which are sieved, and then ground up into finer particles; this process is called “reduction.” Sieving removes air bubbles and provides a particle size that allows for uniform distribution in the finished product.