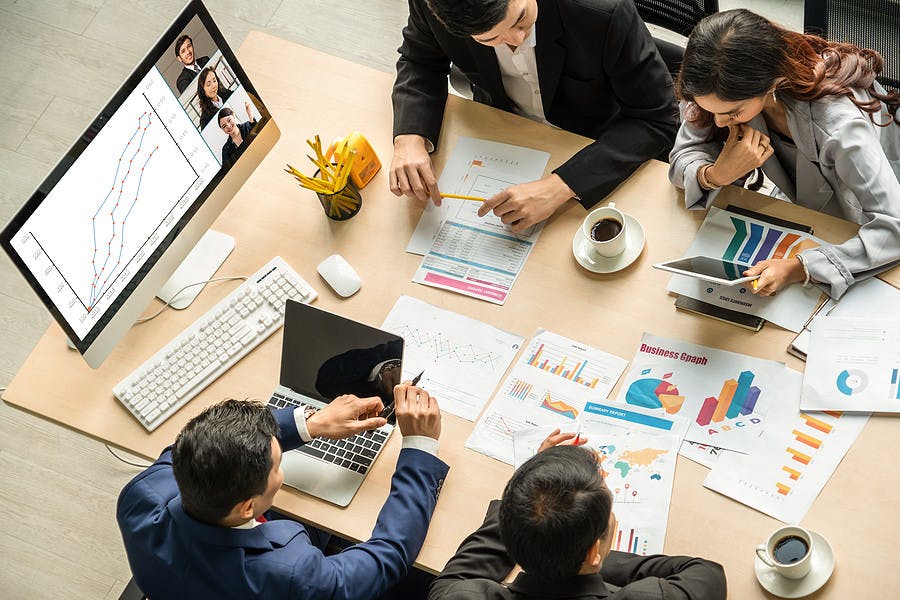
Reliability training is an integral component of any successful business. This aspect encompasses preventive maintenance, managing maintenance operations, and equipment reliability.
By investing in an extensive training program, companies can significantly enhance plant maintenance practices and scheduling and planning procedures. It can ultimately increase effectiveness and profit.
Here we explore steps for creating an effective reliability education program tailored specifically for their organization.
Analyzing your business needs
Before creating an effective reliability training program, it’s crucial to evaluate your organization’s current situation and identify areas that need improvement. The following steps will help you analyze your business needs, establish goals, and ultimately enhance your overall performance in reliability management.
Assessing current reliability levels
To design an effective training program, it is essential first to understand the current state of reliability within your organization. Conduct a thorough reliability assessment, which may involve reviewing maintenance records, evaluating equipment performance, and identifying common failure modes.
Identifying areas for improvement
Once you have assessed your organization’s current reliability, the next step is to pinpoint areas that require improvement. This could involve:
- Streamlining preventive maintenance processes
- Improving maintenance management practices
- Enhancing maintenance of equipment
- Strengthening planning and scheduling procedures
Setting goals and objectives for the program
Establish clear, measurable goals and objectives for your reliability training program. They should be consistent with your business plan and concentrate on tangible improvements. This is to prevent unattainable and confusing goals.
Designing the training program
To improve overall plant performance and efficiency, a comprehensive training program tailored to the needs of maintenance personnel is essential. This program will equip maintenance technicians, supervisors, managers, and production/operations workers with the necessary skills and knowledge to implement best practices and enhance equipment reliability.
Determining the scope of the program
- Target audience: Focus on training maintenance technicians, supervisors, managers, and production/operations workers.
- Topics to be covered: Draft an outline of topics you wish to include during your training program, which could include:
- Preventive maintenance techniques
- Maintenance management best practices
- Effective maintenance of equipment
- Plant maintenance strategies
- Planning and scheduling principles
- Equipment reliability improvement methods
- Reliability assessment tools
Selecting the appropriate training methods
To ensure the effectiveness of the training program, selecting the most suitable training methods is crucial.
- Classroom training: Traditional classroom-based training can be an effective way to deliver reliability training. Learning is enhanced via lectures, discussions, and practical activities.
- Through on-the-job training: Employees can pick up new skills and use them immediately in their place of employment. This can be particularly beneficial when teaching maintenance management and equipment reliability concepts.
- Online training: Online training offers a flexible and convenient option for employees, allowing them to complete courses at their own pace. This method can be particularly useful for covering planning, scheduling, and reliability assessment techniques.
- Workshops and seminars: Hosting workshops and seminars can allow employees to engage with industry experts and learn about the latest best practices in preventive maintenance, plant maintenance, and other relevant topics.
Developing the training curriculum
A well-structured training curriculum is essential for the program’s success, as it improves participants’ understanding and retention of key concepts. Organizing content into focused modules, establishing a logical sequence, and developing a realistic timeline all contribute to this objective.
- Creating modules: Organize the training program into manageable modules, each focused on a specific topic or skill. This will make it easier for employees to absorb and retain information.
- Structuring the program: Determine the most effective training module delivery sequence. Think about elements like the complexity of each topic, prerequisites, and the optimal balance between theory and practice.
- Establishing a timeline: Develop a realistic training program implementation timeline. This should consider the availability of instructors, resources, and employees and the anticipated learning curve.
Implementing the training program
Implementing the training program effectively requires careful consideration of various factors, such as instructor selection, training session organization, and employee participation. By addressing these elements, companies can create an engaging learning environment that promotes the development of essential maintenance and reliability skills among their workforce.
Selecting and training instructors
- Internal vs. external trainers: Choosing internal and external trainers will help you decide whether to use internal resources or pay outside specialists to conduct the training. Budgetary constraints, experience requirements, and expertise availability may influence this choice.
- Train-the-trainer approach: Consider using a train-the-trainer strategy if you employ internal resources. This requires training a few employees who will later inform their coworkers about the initiative.
Organizing training sessions
- Scheduling: Create a schedule that ensures all employees can participate in the training program. This may involve offering multiple sessions, accommodating shift work, or providing online training options.
- Venue selection: Select appropriate venues for the training sessions, considering accessibility, available resources, and the group size.
Ensuring employee participation
- Incentives and motivation: By providing incentives and emphasizing the advantages of enhanced reliability, such as higher productivity and job satisfaction, employers can entice employees to engage in the training program.
- Addressing barriers to participation: Determine and remove any obstacles, such as scheduling problems, language hurdles, or a lack of knowledge about the program, that may hinder employees from participating in the training program.
Monitoring and evaluating the program
Monitoring and evaluating the training program ensures its effectiveness and continued success. Companies can improve their programs by measuring attendance, using assessment tools, and getting feedback.
Tracking progress and performance
- Attendance records: Maintain accurate records of employee attendance at training sessions to track participation and identify any gaps in coverage.
- Assessment tools: Use quizzes, tests, and practical exercises to evaluate employee understanding of the material covered in the training program.
- Feedback mechanisms: Solicit feedback from employees and instructors to gain insights into the program’s effectiveness and identify areas for improvement.
Measuring the program’s effectiveness
- Evaluating results against objectives: Compare the outcomes of the training program to the established goals and objectives to determine its effectiveness.
- Identifying improvement areas: Analyze the training program results to identify areas for further enhancements. This could involve refining the curriculum, adjusting the delivery method, or providing additional support resources.
- Making necessary adjustments: Update the training program to address identified areas for improvement and ensure its ongoing effectiveness.
Continuous improvement and sustainability
Updating and refining the program
- Incorporating new information and best practices: Review and update the training curriculum regularly to reflect the most recent data, industry standards, and innovations in equipment reliability, preventative maintenance, and maintenance administration.
- Addressing changing business needs: The training program should be modified to accommodate changing company requirements such as new machinery, procedures, or legislation.
Encouraging a culture of reliability
- Reinforcing the importance of reliability: Continue to stress the value of dependability and how it affects business performance throughout the training process and ongoing communications.
- Recognizing and rewarding employee achievements: Employees who commit to enhancing reliability, whether through program participation or day-to-day work performance, should be recognized and rewarded.
Conclusion
Any company looking to improve its plant maintenance, planning, and scheduling procedures must invest in developing a reliable reliability training program. Create a thorough training program that considers your company’s requirements and promotes ongoing advancements in equipment dependability and overall business performance using the techniques mentioned in this article.